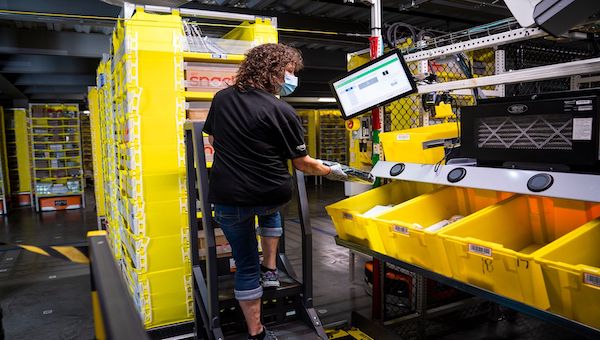
AMAZON SAYS FEWER THAN ONE IN 1,000 ITEMS IT HANDLES IS DAMAGED, THOUGH THE TOTAL NUMBER IS SIGNIFICANT FOR THE RETAILER, WHICH HANDLES ABOUT 8 BILLION PACKAGES A YEAR. PHOTO: LEILA NAVIDI/STAR TRIBUNE/ASSOCIATED PRESS
AMAZON TURNS TO AI TO WEED OUT DAMAGED GOODS
BY: LIZ YOUNGORIGINAL SITE: WSJ
TOPICS
Activism
AI
Belief
Big Pharma
Conspiracy
Cult
Culture
Economy
Education
Entertainment
Environment
Faith
Global
Government
Health
Hi Tech
Leadership
Politics
Prophecy
Science
Security
Social Climate
Universe
War
Company expects artificial intelligence to reduce the number of damaged items moving through fulfillment centers and to speed up deliveries. Amazon.com is rolling out artificial intelligence across a dozen of its largest warehouses to screen items for damage before orders are shipped to customers.
The e-commerce giant said it expects the technology to cut the number of damaged items sent out, speed up picking and packing, and eventually play a critical role in the company’s efforts to automate more of its fulfillment operations.
Amazon warehouse workers are responsible for checking goods for signs of wear and tear as they pick, pack and stow merchandise while meeting company-set targets measuring how many orders they handle per hour. Checking for damage can be time consuming given that most items are in fine condition, said Jeremy Wyatt, director of applied science at Amazon Robotics.
That’s cognitively demanding because obviously you’re looking for something that’s rare and it’s not your primary job,” Wyatt said.
Amazon estimates that fewer than one in 1,000 items it handles is damaged, though the total number is significant for the retailer, which handles about 8 billion packages annually.
The Seattle-based company is adding the technology at a time when retailers, supply-chain operators and software makers are searching for ways to use AI to speed up workflows and simplify supply-chain decision making. Amazon has been working to further automate its warehouses as it has struggled to find workers and looked to turn some of the most physically challenging and repetitive warehouse jobs over to robots.
Amazon’s rollout is part of a broader push across the corporate world to bring more AI technology to logistics operations as companies try to manage complicated supply chains while keeping goods moving rapidly and reliably.
Logistics operators automating their warehouses have to build technology to take over jobs that are typically simple for humans, from picking and packing items to checking them for damage, said Rueben Scriven, research manager for the warehouse automation sector at research firm Interact Analysis.
For warehouse workers today, “when you’re decanting a case into totes, it’s a manual process,” Scriven said. “It’s very easy for someone to check if this is damaged or not. But if you wanted to automate that process, you then have to also find a way to identify where damaged items are.”
For Amazon, reducing the number of damaged goods that ship out is crucial to improving the customer experience.
Amazon so far has implemented the AI at two fulfillment centers and plans to roll out the system at 10 more sites in North America and Europe. The company has found the AI is three times as effective at identifying damage as a warehouse worker, said Christoph Schwerdtfeger, a software development manager at Amazon.
The AI checks items during the picking and packing process. Goods are picked for individual orders and placed into bins that move through an imaging station, where they are checked to confirm the right products have been selected. That imaging station will now also evaluate whether any items are damaged. If something is broken, the bin will move to a worker who will take a closer look. If everything looks fine, the order will be moved along to be packed and shipped to the customer.
Amazon trained the AI using photos of undamaged items compared with damaged items, teaching the technology the difference so it can flag a product when it doesn’t look perfect, Schwerdtfeger said.